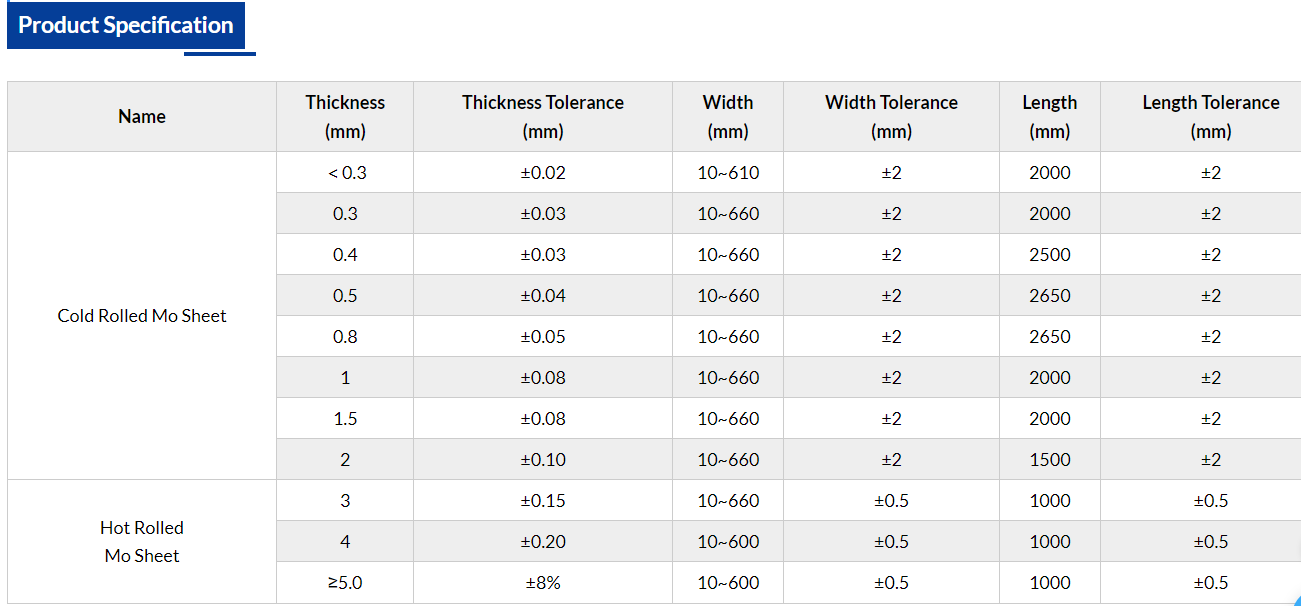
Product Physical And Chemical Properties
1) High purity: Mo content ≥99.95%.
2) High density: ≥10.2g/cm3
3) High melting point: 2620℃ (4753°F)
4) Low coefficient of thermal expansion: (0-1600℃): 6×10^-6/℃
5) High yield strength: (1600℃): 50MPa
6) High flatness: ≤3.2%
7) High thermal conductivity: 135w/m. k
8) Excellent corrosion resistance against molten metal s and glass
9) Good creep resistance
10) Good electrical conductivity
Application
1) Aerospace:
Mo sheet can be used as high-temperature structural materials and heat shields. It can be used to manufacture engine parts, combustion chambers, nozzles, missile shells, etc. for aerospace vehicles. In addition, it is also used to manufacture thermal conductive components and radiation shields for aircraft.
2) Nuclear energy:
It is widely used in key components of nuclear reactors for manufacturing structural materials, nuclear fuel cladding, reactor core materials, etc. of nuclear reactors. Mo sheet can also be used to manufacture radiation protection equipment, nuclear fuel processing equipment, etc.
3) Electronics industry:
Mo sheets are often used as etching and deposition targets in semiconductor manufacturing. They can be used to manufacture substrates, packages, vacuum packages, etc. For electronic components. In addition, mo sheets can also be used to manufacture thin film submicrostructure vacuum equipment, vacuum tubes, etc. of semiconductor devices.
4) Optics and sensors:
The excellent thermal conductivity and stable thermal expansion characteristics of mo sheets make them suitable for precision optical components and sensors. In these applications, special attention should be paid to the surface treatment and precision control of moly sheets.
5) Chemical and oil and gas:
It can be used to manufacture chemical equipment, oil drilling pipes, pipelines, valves, etc. In addition, moly sheet can also be used to manufacture petroleum refining equipment, catalyst carriers, etc., as well as chemical reactors, storage tanks, etc.
6) Other applications
Moly sheet are also used to manufacture lithium batteries, food processing equipment, medical equipment, glass and ceramic products, magnetic materials, electroplating equipment, etc.
Production Process
The tungsten and molybdenum products produced by our company are all produced by powder metallurgy method, which is also the traditional method for preparing moly sheets.
First, the molybdenum powder is pressed into a predetermined shape and then sintered at high temperature. During this process, the powder particles will fuse to form a solid structure. Powder metallurgy can effectively control the thickness and size of the moly sheet and is suitable for producing moly sheets of various specifications.
Generally speaking, there are two main manufacturing processes for moly sheet: hot rolling and cold rolling. Hot-rolled moly sheets are rolled into plates by heating molybdenum blocks blanks at high temperatures through rolling machinery equipment, so they have higher strength and wear resistance, and are suitable for use under high-strength and high-temperature conditions; while cold-rolled moly sheet are rolled into plates or sheets by rolling mills at room temperature, so they have better surface smoothness and dimensional accuracy, and are suitable for applications with high surface requirements.
After rolling with a deformation of more than 60%, the density of the moly sheet is basically close to the theoretical density of molybdenum. Therefore, it has high strength, uniform internal structure and excellent high-temperature creep resistance. It is widely used in the production of reflective screens and cover plates in sapphire crystal growth furnaces, reflective screens, heating belts, connectors in vacuum furnaces, sputtering targets for plasma coating, high-temperature resistant boats and other products.